The fully continuous pyrolysis plant is specifically designed to ensure safety, profits, and is environmentally friendly. Not only can this machine work continuously for 24 hours, but it can also feed raw materials on one side and then discharge the final products on another side. Generally speaking, the continuous pyrolysis plant can work with rubber, waste tyre, medical waste, plastic, and oil sludge. And the tyre pyrolysis plant is very popular around the world.
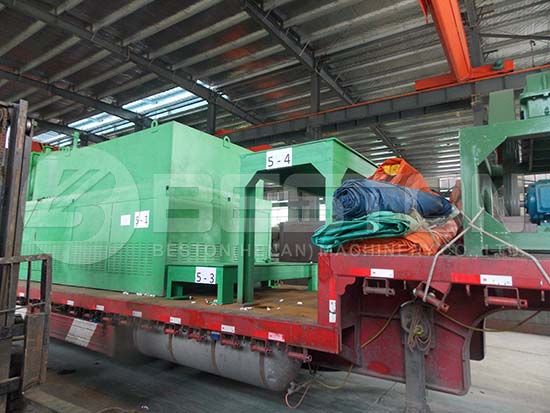
Continuous Pyrolysis Plant Romania
Technical Benefits of Continuous Pyrolysis Plant
1. Manageable electrical control system. Typically, this control system comes with a pressure gauge, thermometer, an emergency stop device, etc. It’s possible to monitor the working condition of the entire plant to ensure the machine is running optimally. Indeed, it saves labor costs for investors.
2. Screw feeding sealing system. The continuous pyrolysis machine implements screw feeding sealing system technology, and the company’s invention patents hold this. And this technology will often stop the heat from spreading. Furthermore, this screw technique ensures uniform feeding.
3. Unique dedusting system. Basically, this means that it produces zero-emission pollution. The environmental standard is stricter in some countries. In most cases, the dedusting system will take place in three steps to ensure that the discharged waste smoke adheres to the relevant emission requirements. These three procedures include ceramic ring adsorption, water rinsing, and water spraying. Below is a Beston pyrolysis plant in the Philippines.
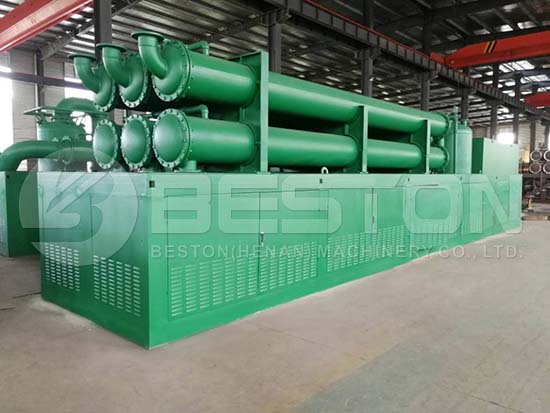
Continuous Pyrolysis Machine to the Philippines
In order to guarantee safety and cost-effectiveness for customers, this continuous tyre pyrolysis plant comes with a circulation heating system, a moving horizontal pyrolysis reactor, a robust dedusting system, etc.
Continuous Tyre Pyrolysis Plant’s Operation Description
– Pre-treatment. Pre-treatment of the waste materials is necessary before entering the pyrolysis process. A tyre shredder machine is required to crush those tyres into 20 mm pieces. It also requires to crash the plastics, especially if they’re large and rigid. In case the humidity of medical waste and plastics is extremely high, it requires a dryer.
– Feeding raw materials. Having been pretreated, feed the waste materials into the reactor. Ensure the feeding inlet door is sealed tightly, and ensure there’s no gas leakage as well.
– Pyrolysis. By using wood, fuel gas, charcoal, coal, etc. as heating materials, heat the pyrolysis reactor. The reactor will be gradually heated, and once the temperature reaches a certain temperature, the oil gas will be created. Of course, the pyrolysis plant cost will be different from the working method, capacity, etc.
– Condensing. The condensing system receives the oil gas from the reactor and condenses it to liquid oil.
– Waste gas recovery. Through a safety device, the gas that can’t be liquefied will be made to return to the combustion system.
– Discharge. Typically, the carbon black and steel wire will be discharged automatically. Below a video for your reference.
Various Applications of Final Pyrolysis Products
1. Tyre oil
– It can be very useful as industrial fuel materials when it comes to burning
– It can assist in relieving energy crisis
– If further refined to gasoline or diesel by waste oil distillation machine, this oil can be useful in low-speed engines, including a digging machine, loading machine or road roller, etc.
2. Carbon black
– It can be useful as fuel or construction bricks with clay
– It can be further made into briquette or pellet for burning or even further processed to make cable jackets, pipes, and so on.
3. Steel wire
– It can be used, or further reprocessed, to make iron and steel rod.